PROJECT 2: Omnidirectional Soft Robotic Arm for Vascular Intervention Surgery (VIS) - COMPLETED
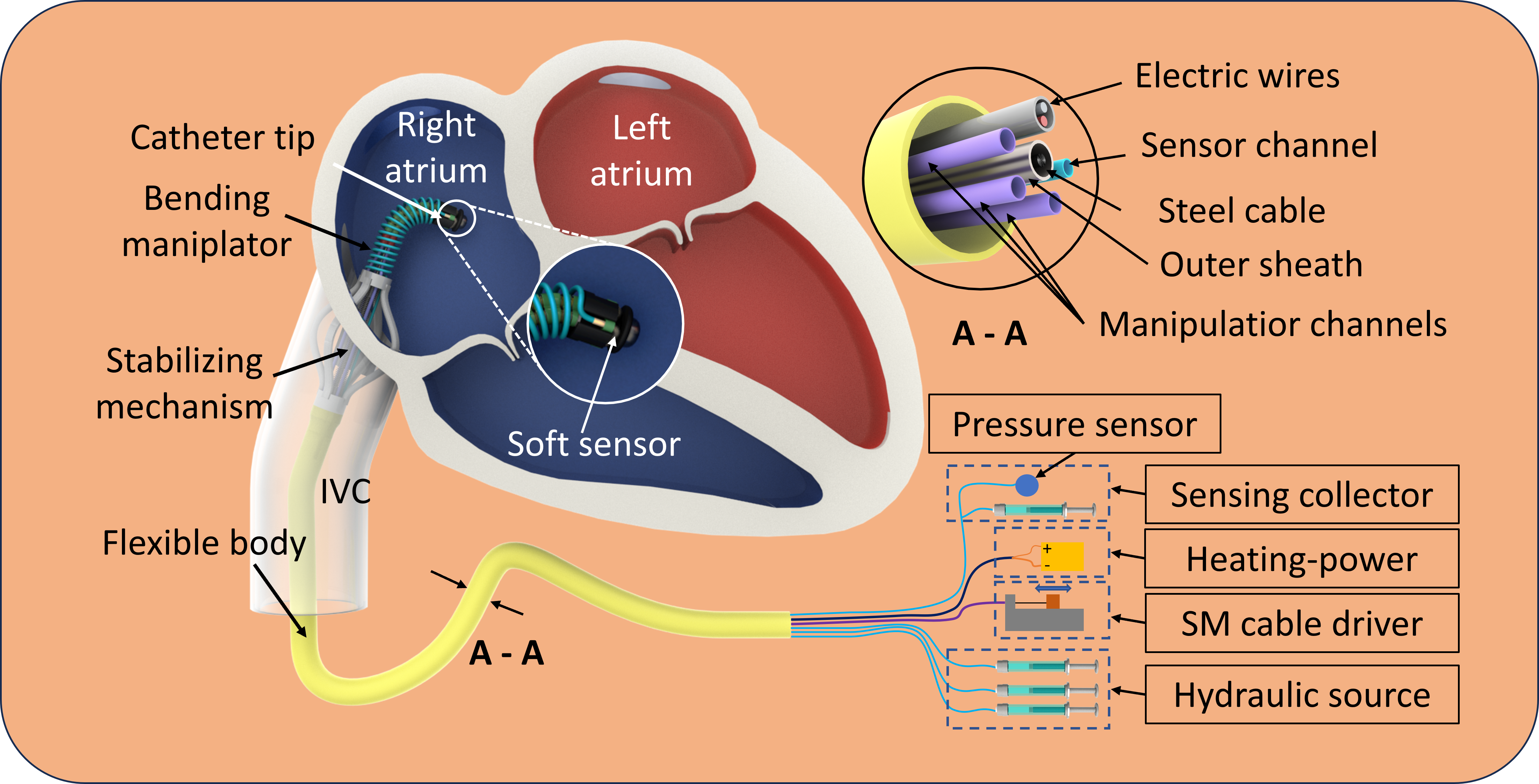
Software: Solidworks, MATLAB, and CURA;
Hardware: QPIDe Data Acquisition Device (Quanser), Magnetic Tracking System (trakSTAR - TRACKLAB), Pressure Sensors 40PC250G2A (Honeywell), Linear Motors (Zaber X-LRQ-E Series), Load Cell – LSB200 (FUTEK), and Electrosurgical Unit (Led Surtron 120, Stark Medical);
Skills: Mechanical design, Prototyping, Mathematical Modeling (Soft Actuators), and Image Processing.
Design and Working Principle - PDF
For protyping this SRA, I used three HFAMs being arranged 120 degrees apart and contrained by a layer comprised of ultrathin-wall heat shrink (Fig. A), thereby endowing the system with three degrees of freedom (3-DOFs). This SRA's working principle is elegantly straightforward: any deviation in pressure among the HFAMs results in the bending of the SRA, while uniform pressures across all HFAMs induce elongation. The inherent flexibility of the SRA facilitates its navigation into intricate chambers and corners (Fig. B). Through the formulation of a mathematical model, the operational workspace of the SRA was elucidated, which is a set of concentric spheres with increasing radii and partially missing bottom areas (Fig. C-D). This workspace was then validated by the use of a magnetic tracking system.
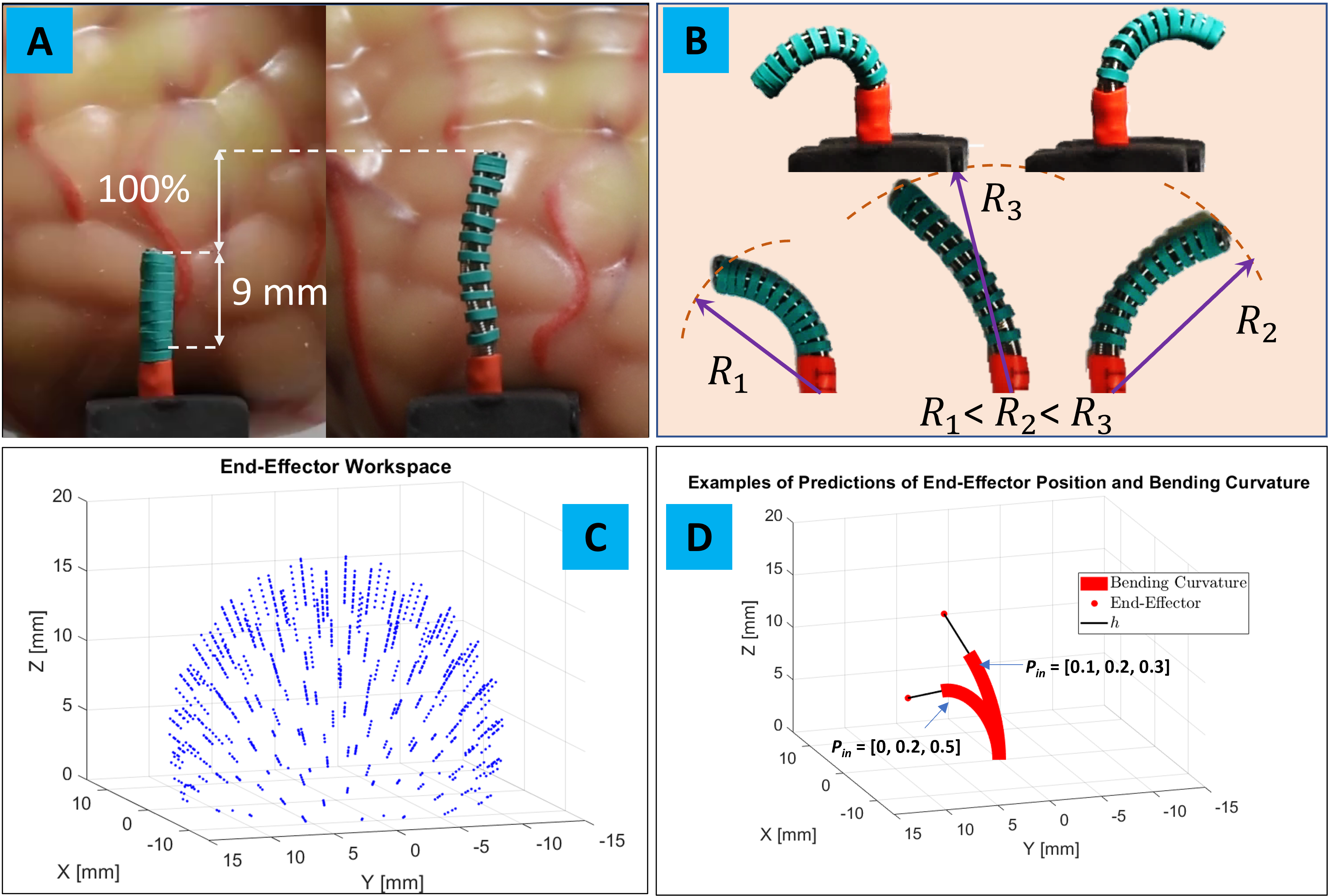
Demonstration and Validation
I conducted an experiment to validate the feasibility of the SRA performing the prevailing cardiac ablation in the heart's right atrium (RA). A phantom model representing the inferior vena cava (IVC) and RA was employed, incorporating a small porcine tissue specimen (Fig. A). The procedure involved the insertion of the SRA into the IVC, with the stabilizing mechanism activated upon the SRA's tip reaching the RA, thereby ensuring tip stability (Fig. B-C). Subsequently, the ablation procedure was carried out prior to the retraction of the SRA from the simulated cardiac environment (Fig. D).
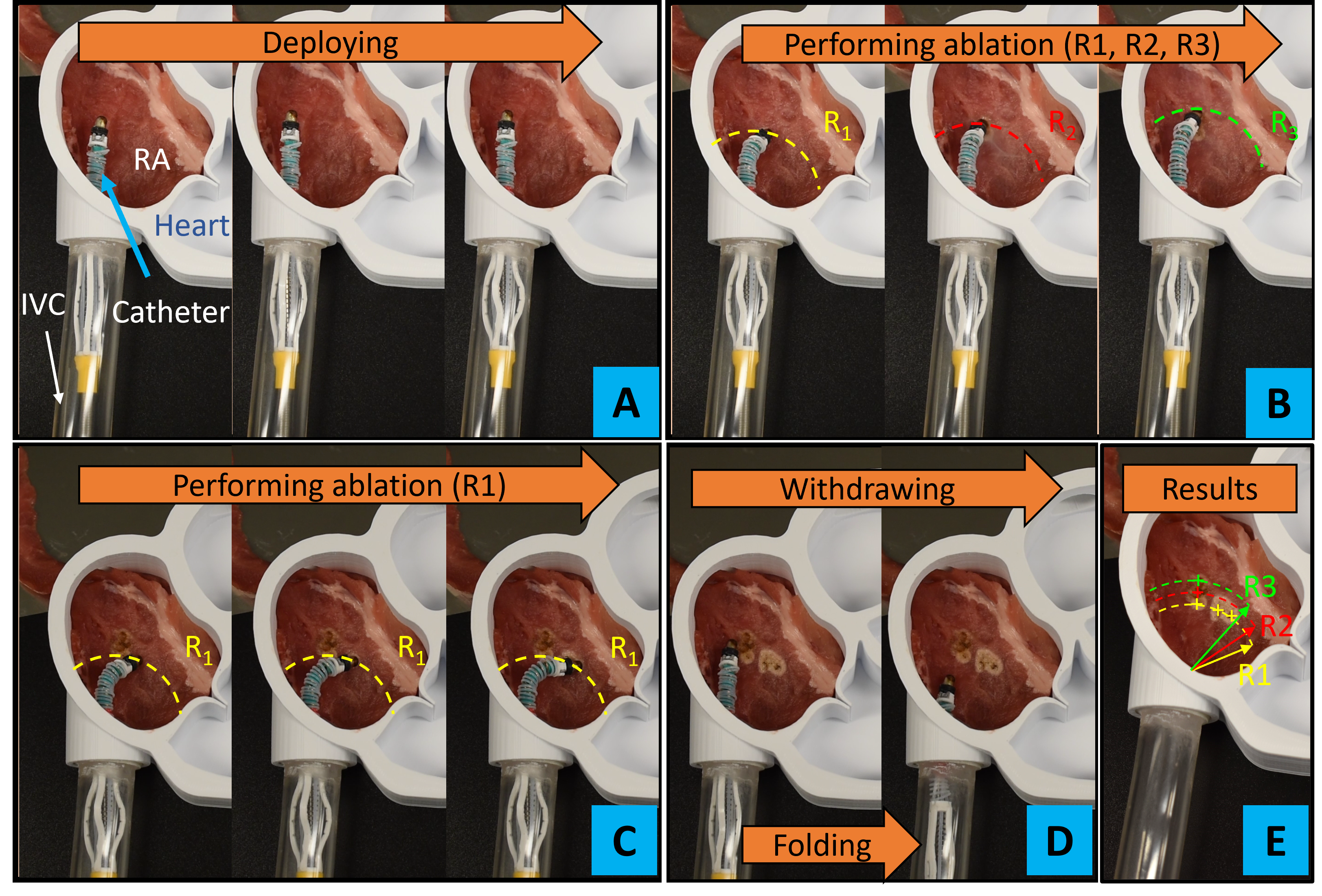
Media